Why Illustrated Parts Catalogs Are Essential for Modern Equipment Maintenance
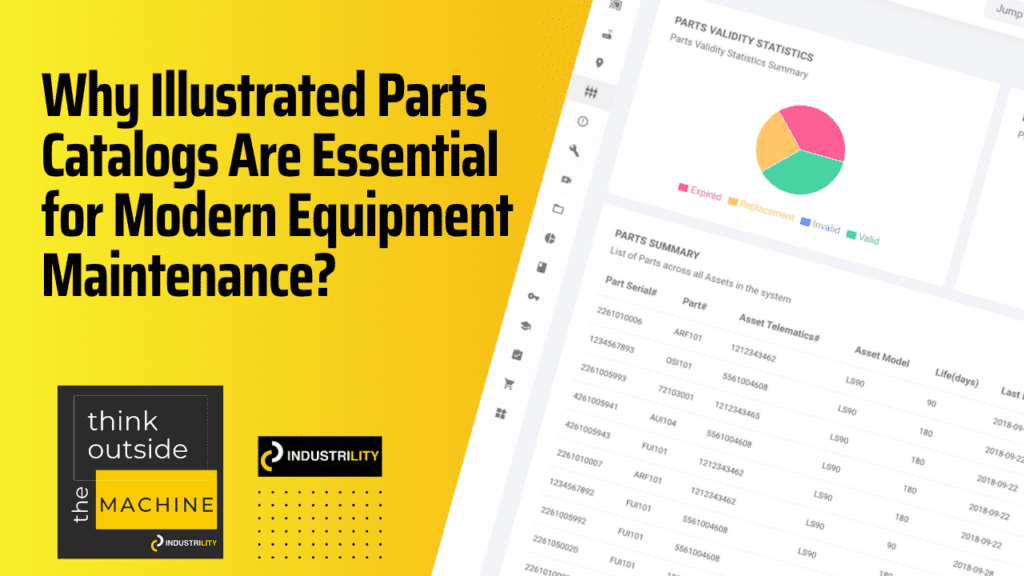
In today’s rapidly changing industrial environment, equipment uptime is essential. Whether it’s construction, material handling, or manufacturing, the ability to maintain complex machinery efficiently can have a direct impact on a company’s revenue. Amid growing complexity in equipment design, one of the tools that is quietly revolutionizing aftersales support and maintenance operations—the illustrated parts catalog.
This visual documentation tool has come a long way from printed manuals and PDFs. Today, electronic parts catalogs (EPCs) and 3D parts catalogs enable faster troubleshooting, reduce ordering errors, and improve customer satisfaction. But what exactly makes illustrated catalogs so effective—and why should manufacturers invest in them?
What Is an Illustrated Parts Catalog?
An illustrated parts catalog is a visual guide that breaks down complex machinery into its component parts using visualizations. Each component is labeled with part numbers, descriptions, and sometimes pricing or inventory data. Traditionally used in service manuals, these catalogs have now evolved into interactive digital platforms with hyper-personalized capabilities.
Depending on the solution, users can:
- Zoom into assemblies
- Click on individual parts to see specifications
- View associated documentation (manuals, videos, etc.)
- Order parts directly through the interface
This interactive nature reduces the guesswork and boost parts identification by 70%—particularly useful in industries where downtime is costly.
Why Traditional Manuals Fall Short
Despite technological advancements in engineering, many manufacturers still rely on PDFs or printed manuals to guide maintenance teams and customers. These methods often lack clarity, are hard to navigate, and quickly become outdated. Worse, they frequently lead to ordering errors due to misidentification of parts, which delays repairs and drives up service costs.
Moreover, in multilingual or globally distributed environments, textual documentation alone may not be sufficient. Visuals bridge that gap by offering a universal language, enabling technicians and customers to understand machinery without relying heavily on translation or prior technical knowledge.
The Advantages of Electronic and 3D Parts Catalogs
The shift from paper-based to electronic parts catalogs has added a new layer of efficiency and accessibility. Digital catalogs can be updated in real-time, integrated with inventory systems, and accessed from mobile devices, making them invaluable in field service scenarios.
Some advanced platforms, like Industrility, even support 3D parts catalogs, allowing users to rotate, zoom, and interact with fully rendered machine assemblies. This immersive experience not only improves part identification but also enhances training and onboarding for new technicians.
Benefits at a Glance:
- Faster part identification and ordering
- Reduction in support queries and ordering errors
- Real-time updates for part availability and pricing
- Seamless integration with ERPs or service platforms
- Improved training and knowledge transfer
Real-World Application: Astec’s Aftersales Transformation
A compelling example of the impact of visual catalogs can be seen in Astec, a leading manufacturer of asphalt equipment. Faced with the need to streamline support for their customers, Astec adopted a digital parts and service platform powered by Industrility.
By implementing an illustrated parts catalog that was accessible to both customers and partners, Astec was able to simplify parts lookup and ordering. This not only improved the end-user experience and reduced internal workloads by minimizing support queries and misorders, but also led to an 82% increase in efficiency for parts identification—ultimately boosting the quote-to-order win rate.
The transition to a visual, digital parts catalog allowed Astec to build stronger relationships with their partner network, improve operational efficiency, and ultimately support their customers better and faster.
Getting Started: What to Consider
If you’re a manufacturer exploring illustrated parts catalogs, here are a few considerations to help guide the transition:
- Data Accuracy: Ensure the engineering and parts data feeding the catalog is reliable and well-maintained.
- User Experience: Choose a platform that is intuitive for both technicians and non-technical users.
- Integration Capabilities: Look for solutions that can connect with your existing ERP, CRM, or service tools.
- Scalability: Make sure the system can grow with your product line and adapt to future needs like AR or IoT integration.
Industrility offers tools that simplify this transition, making it easier for manufacturers to build and launch digital catalogs tailored to their needs—whether it’s a traditional EPC or a more immersive 3D parts catalog.
Conclusion
In an industry where equipment downtime can cost thousands per hour, improving the accuracy and speed of part identification is no longer optional—it’s essential. Illustrated parts catalogs offer a clear path to reducing service friction, empowering users, and enhancing aftersales support.
As machinery continues to evolve, so should the tools we use to maintain it. A well-designed illustrated parts catalog doesn’t just improve operations—it elevates the entire customer experience.
Ready to transform your maintenance experience with a visual-first approach? Learn how the Industrility Parts App can help you launch your own illustrated parts catalog and enhance your aftersales operations today.